汽車電路板
汽車PCB產品

4層噴錫汽車燈板PCB線路板
層數:4
板材:FR4 TG170
板厚:1.6mm
表面處理:無鉛噴錫
內外完成銅厚:1/1oz
最小孔徑:0.5mm
內層線寬線距:16.8/13.8mil
外層線寬線距:16.1/13.8mil
應用產品:汽車燈板

6層噴錫FR4汽車印制線路板
層數:6
板材:FR4 TG150
板厚:2.0mm
表面處理:無鉛噴錫
內外完成銅厚:1/1oz
最小孔徑:0.3mm
內層線寬線距:6.9/4mil
外層線寬線距:6.9/4mil
應用產品:汽車板

6層FR4 KB噴錫汽車印刷電路板
層數:6
板材:FR4 KB TG150?
板厚:2.0mm
表面處理:無鉛噴錫
內/外完成銅厚:3/3oz
最小孔徑:0.6mm
內層線寬線距:20/20mil
外層線寬線距:20/20mil
應用產品:寶馬UL19.2kW雙向母線電容板

4層生益無鹵沉金阻抗PCB板
層數:4
板材:FR4 生益 1150G 無鹵
板厚:1.0mm
表面處理:沉金1U
特殊工藝:阻抗、二維碼、序列號
最小孔徑:0.2mm
內層線寬線距:8.8/6.5mil
外層線寬線距:7.8/7.8mil
應用產品:汽車板

4層噴錫汽車USB 充電器PCB板
層數:4
板材:FR4
板厚:1.2mm
表面處理:無鉛噴錫
內外完成銅厚:1/1oz
最小孔徑:0.3mm
內層線寬線距:8.9/4.2mil
外層線寬線距:8.9/4.2mil
應用產品:USB 充電器

4層FR4噴錫汽車電子PCB線路板
層數:4
板材:FR4
板厚:1.6mm
表面處理:無鉛噴錫
內外層完成銅厚:2/2oz
最小孔徑:0.55mm
內層線寬線距:/
外層線寬線距:15/21mil
應用產品:汽車產品
汽車電路板的分類
車體電子控制系統
發動機控制系統
點火控制系統
燃油控制系統
空氣供給系統
車身控制系統
電源管理系統
安全管理系統
燈光照明系統
顯示監控系統
底盤控制系統
ABS控制系統
電子穩定系統
胎壓監測系統
轉向控制系統
車載電子控制系統
車載電視
行車記錄儀
倒車雷達系統
車載導航系統
車載攝像系統
汽車電動化和智能化將是核心驅動力
對應24GHz系統的高頻基材
- 廠家
- 產品牌號
- 樹脂組成類型
- Dk(10GHz以下)
- Df(10GHz以下)
- Dk熱變化率 ppm/℃
- Rogers
- RO4835
- 碳氫化合物
- 3.48±0.05
- 0.0037
- +50(-50~150℃)
- Taconic
- TLF-35A
- PTFE
- 3.5
- 0.0016
- -
- 生益科技
- S7136H
- 碳氫化合物
- 3.42±0.05
- 0.003
- -
對應77GHz (或79GHz)系統的高頻基材
- 廠家
- 產品牌號
- 樹脂組成類型
- Dk(10GHz以下)
- Df(10GHz以下)
- Dk熱變化率 ppm/℃
- Rogers
- RO3003
- PTFE+陶瓷(無玻纖)
- 3±0.04
- 0.001
- -3 (-50~150℃)
- Taconic
- TSM-DS3
- PTFE
- (Tk) 5.4 (-30~120℃)
- 0.0011
- (Tk) 5.4 (-30~120℃)
- Taconic
- TAL-28
- PTFE+納米填料
- 2.8
- 0.0012
- (Tk) 2.24(-30~120℃)
- 生益科技
- GF77G
- PTFE
- 2.28±0.04
- 0.0012
- -
汽車電子4大系統與子系統
- 系統
- 子系統
- PCB占比
- 動力控制系統
- 點火控制系統、燃油噴射控制系統、發動機怠機控制系統、廢氣再循環系統、防抱死控制系統
- 50%
- 安全控制系統
- 自動變速器控制系統、懸架電子系統、動力轉向電子控制系統、巡航控制系統
- 22%
- 車身電子系統
- 自動空調系統、電子儀表系統、安全氣囊系統、汽車電子防盜系統、抬頭顯示系統
- 25%
- 娛樂通訊系統
- 電子儀表系統,汽車音響系統、車載導航系統、電子地圖系統
- 3%
毫米波雷達對PCB基材的要求如下:
毫米波雷達包括兩大核心硬件:MMIC電路和雷達天線高頻PCB板,在基材的選擇和PCB的加工制作上都有很高的要求。基材需要選用高頻材料。高頻PCB板的生產,對廠家工藝控制能力,比如銅厚、線寬的容差要求都更高。毫米波雷達用的PCB價格一般是普通PCB價格的1.5-3倍。
新能源汽車PCB用量和價值量
新能源汽車PCB用量和價值量大幅提升。傳統汽車現階段對PCB的需求量較小,PCB價值量也比較低,主要是動力系統需求PCB最多,占比達32%。 對比來看,傳統汽車平均每輛汽車PCB用量約1平方米,價值量約60美元, 高端車型PCB用量在2-3平方米,價值量約120-130美元,而新能源汽車PCB 單車用量接近8平米,單車價值量高達400美元。
PCB常見負荷和失效模式
PCB 是這些電子系統的關鍵部件,必須特別注意可能會導致短路或開路的 PCB失效模式。可靠性是汽車對PCB的核心要求。在一輛由幾百伏的電壓提供動力的無人駕駛汽車中,必須徹底了解其中的 PCB失效模式以保證可靠運行。
可能的失效模式
- 1.鍍通孔可內銅層裂紋
- 2.外銅層裂紋
- 3.微導孔裂紋
- 4.半固化片裂紋
- 5.PCB表面電化學遷徙
- 6.阻焊膜裂紋
PCB環境負荷
- 1.溫度循環及貯存
- 2.彎曲
- 3.震動
- 4.濕度
- 5.幾種負荷的組合
PCB的組裝負荷
- 1.回流焊
- 2.選擇焊
- 3.壓合技術
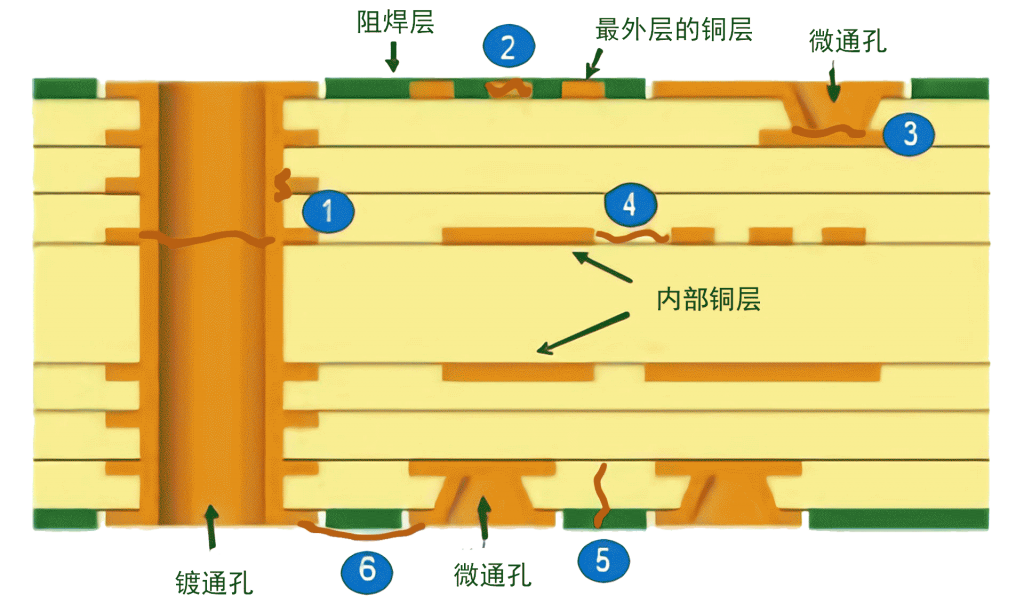
匯和電路深知汽車電子的可靠性等同于汽車的可靠性,因此需確保汽車電子的可靠性滿足使用壽命與環境耐受性要求:
- 汽車電子系統所用PCB需經受多種環境變化的考驗,例如溫濕度、氣候、酸霧、振動、電磁干擾、電流沖擊等;
- 為保障正常壽命周期,PCB需要符合高可靠性、高集成度、高散熱、大電流(厚銅)、輕量小型化、埋置器件等特點和要求。例如:新能源電動汽車的高壓控制系統,通過使用強電流板,將原來零散的高壓器件部位、分散的DC/充放電/MCU等功能部位集成在一塊PCB上,密集程度翻了幾倍,卻在結構空間要節省30%。
匯和電路采取如下措施確保汽車電子用PCB提高可靠性:
- 通過IATF16949汽車質量管理體系標準;
- 選擇合適的材料與生產工藝、可靠性檢測與試驗;
- 在工程策劃之時,根據汽車電子產品使用部位選擇合適的材料;
- 嚴格遵照控制計劃的要求生產、監測、記錄;
- 關鍵工序、關鍵特性運用SPC監控、分析;
- 確保工藝參數的穩定性,生產過程的可追溯性;
- 以IPC-TM-650標準為基礎,建立了一套系統、嚴格的產品性能測試方法和評價機制,包括熱循環實驗、高溫熱沖擊、鹽霧試驗、大電流沖擊、耐高壓、電遷移等。
為什么選擇匯和電路?
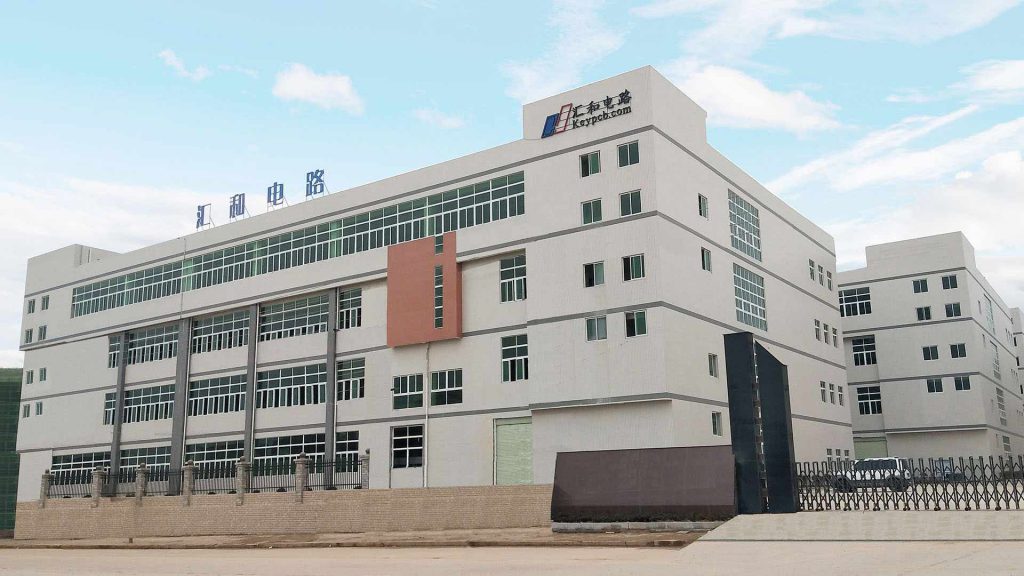
匯和電路擁有12000平方米生產車間,現在職高級工程師20+人以上,月產能3.5萬㎡,是一家專業生產制造PCB電路板廠家。 匯和電路獲得UL、CUL、ISO9OO1、IATF16949、ISO14001、ISO13485、ISO45001、RoHS、REACH、POPs、PFAS等管理體系和產品的認證,符合IPC國際檢驗標準。

匯和電路一直在不斷努力提高PCB電路板的質量以求接近完美無瑕,匯和電路不僅有嚴格完整的品管系統,還具備精密的生產和測試設備。匯和電路專業周到的服務能力以及完整的品管系統為匯和電路在客戶中贏得了良好的信譽。
優質進口原材料,從源頭保障產品品質
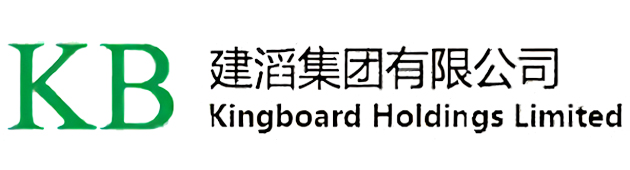
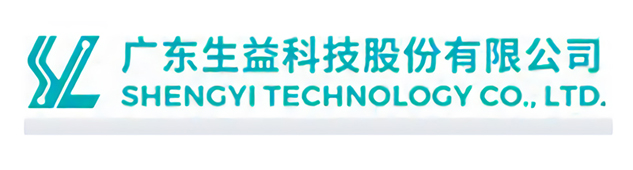
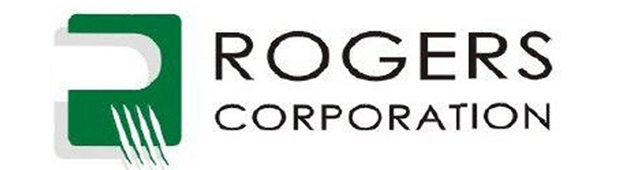
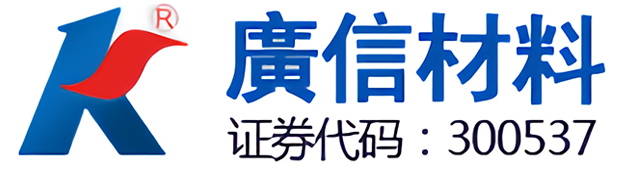

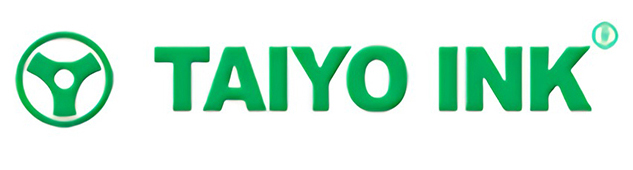